Unlocking Operational Excellence: A Deep Dive into the World of Lean Management
- Aryan Agarwal
- Dec 28, 2023
- 3 min read
In the dynamic realm of business, staying ahead of the competition requires more than just keeping up with the latest trends. It demands a strategic approach that not only streamlines processes but also maximizes efficiency and minimizes waste. This is where Lean Management steps into the spotlight, offering organizations a proven framework for achieving operational excellence. In this blog, we'll embark on a journey into the core principles, real-world applications, and transformative impact of Lean Management.
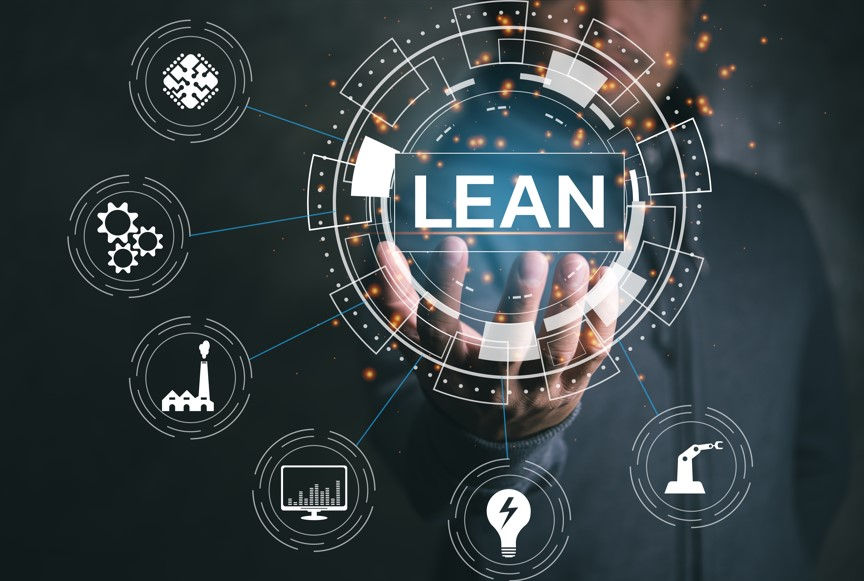
Understanding Lean Management:
Lean Management is a philosophy that strives to create more value for customers with fewer resources. Originating from the manufacturing practices at Toyota in the 20th century, Lean has transcended its industrial roots and is now a beacon for various industries seeking to optimize their operations. Lean management involves the following concepts:
Value Stream Mapping:
Lean starts with understanding the entire value stream of a product or service. Value stream mapping involves visualizing every step, from concept to delivery, allowing organizations to identify inefficiencies and areas for improvement.
Just-In-Time (JIT):
JIT is a pivotal concept in Lean Management, emphasizing the production of goods or services at the exact moment they are needed. This reduces excess inventory, cuts down on carrying costs, and promotes a more responsive and agile workflow.
Continuous Improvement (Kaizen):
A cornerstone of Lean Management is the commitment to continuous improvement, known as Kaizen. This involves fostering a culture where every employee actively contributes to identifying and implementing small, incremental changes that collectively lead to significant improvements.
Respect for People:
Lean recognizes the significance of a motivated and engaged workforce. By empowering employees and respecting their insights, organizations create an environment where innovation and collaboration flourish.
Pull Systems:
Unlike traditional push systems based on forecasts, Lean employs pull systems where products or services are produced in response to actual customer demand. This minimizes overproduction and aligns production with real-time needs.
Applications of Lean Management:
Lean Management has transcended its manufacturing origins and found success in various sectors:
Lean in Services:
Service industries have adopted Lean principles to enhance customer experiences, streamline processes, and eliminate inefficiencies. From banking to hospitality, Lean has proven its versatility in delivering value beyond the manufacturing floor.
Lean Healthcare:
In the healthcare sector, Lean has been a catalyst for improving patient care, reducing waiting times, and optimizing administrative processes. By focusing on patient value and minimizing waste, Lean Healthcare transforms the delivery of medical services.
Lean in Software Development:
Agile methodologies in software development share common ground with Lean principles. Iterative development, continuous testing, and customer collaboration align seamlessly with Lean's commitment to delivering value and adapting to changing requirements.
Impact of Lean Management:
Implementing Lean Management principles yields a number of benefits:
Increased Efficiency:
Lean processes are designed to minimize waste, resulting in streamlined workflows and increased operational efficiency. This enables organizations to respond promptly to customer demands.
Cost Reduction:
By targeting and eliminating waste, Lean Management reduces production costs and minimizes inventory holding costs. This cost-effectiveness enhances a company's competitiveness in the market.
Improved Quality:
Lean principles focus on identifying and eliminating defects at their source. Continuous improvement and rigorous quality control lead to a higher overall quality of products and services.
Enhanced Customer Satisfaction:
Lean Management places the customer at the center of its philosophy. By delivering value through efficient processes, organizations can significantly improve customer satisfaction and loyalty.
Employee Engagement:
Lean's emphasis on continuous improvement and respect for people creates a culture of engagement and empowerment among employees. This not only boosts morale but also fosters a more innovative and productive workforce.
Challenges and Considerations:
While Lean Management offers a transformative framework, it's not without challenges. Organizations must navigate resistance to change, sustain improvements over time, and instill a cultural shift to fully embrace Lean principles. The implementation of Lean is context-dependent, requiring a tailored approach to fit the unique needs of each organization.
In the end, I would like to conclude that Lean Management is not just a set of principles; it's a mindset that champions efficiency, continuous improvement, and customer-centricity. As businesses navigate the complexities of the modern landscape, Lean stands as a beacon, guiding organizations towards operational excellence. By embracing Lean Management, companies can unlock their full potential, reduce waste, enhance customer satisfaction, and build a foundation for sustainable success in an ever-evolving business landscape.
Comments